Moulding tolerances and surface finish are critical aspects of on-demand production, directly impacting the quality and functionality of the final product. Understanding what to expect from on-demand production is essential for manufacturers, designers, and engineers to ensure seamless project execution.
Moulding in On-Demand Manufacturing: A Deeper Dive
On-demand manufacturing has revolutionized the moulding process, offering unparalleled flexibility, speed, and precision. This approach enables the rapid production of moulded parts without the need for large-scale tooling or inventory storage.
Benefits of Moulding in On-Demand Manufacturing
With on-demand manufacturing, you can rapidly create moulds, which cuts down lead times from weeks to days, allowing for quicker production. Moulding offers modifying designs or iterating on existing ones without incurring significant tooling costs, providing flexibility in the production process. It is easier to avoid the necessity for large-scale tooling investments or the need for extensive inventory storage, streamlining the manufacturing process. Moulding can employ advanced technologies and precise tooling to consistently produce high-quality parts, ensuring reliability and durability. You can adjust production levels easily, scaling up or down based on demand, allowing for efficient resource utilization.
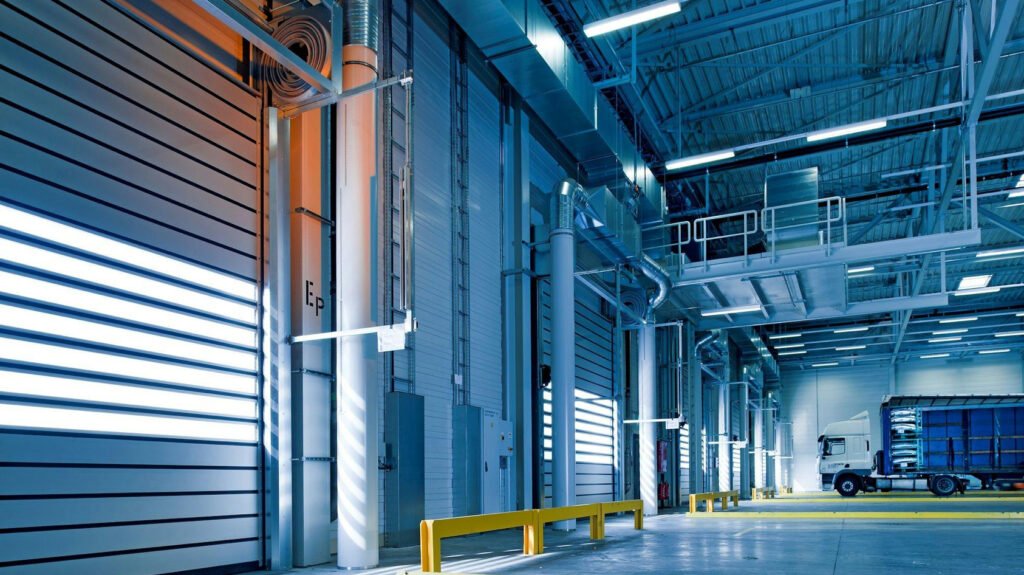
Common Moulding Techniques in On-Demand Manufacturing
- Injection Moulding: Ideal for high-volume production of complex parts with tight tolerances.
- CNC Machining: Suitable for producing small to medium-sized parts with intricate geometries.
- 3D Printing: Enables rapid prototyping and production of complex, customized parts.
- Reaction Injection Moulding (RIM): Perfect for producing large, lightweight parts with smooth surfaces.
Materials Used in On-Demand Moulding
- Plastics: Thermoplastics, thermosets, and elastomers for various applications.
- Metals: Aluminum, steel, and other metals for strong, durable parts.
- Composites: Carbon fibre, glass fibre, and other materials for high-performance applications.
" "
Applications of On-Demand Moulding
- Aerospace: Lightweight, high-performance parts for aircraft and spacecraft.
- Automotive: Rapid prototyping and production of complex automotive components.
- Medical: Customized, precise parts for medical devices and equipment.
- Consumer Products: Rapid production of customized parts for various industries.
By leveraging on-demand manufacturing for moulding, businesses can streamline their production processes, reduce costs, and bring innovative products to market faster.
Moulding Tolerances: Understanding the Limits
Moulding tolerances refer to the acceptable variations in the dimensions of a part produced through injection moulding or other manufacturing processes. These tolerances are crucial in ensuring proper fit, function, and assembly of components. On-demand production typically offers tighter tolerances than traditional manufacturing methods, thanks to advanced technologies and precise tooling.
Surface Finish: Aesthetic and Functional Considerations
Surface finish is another vital aspect of moulding, influencing both the appearance and performance of the final product. On-demand production offers various surface finish options, including textured, smooth, or matte finishes. The chosen surface finish can impact the product’s durability, corrosion resistance, and overall user experience.
Factors Influencing Moulding Tolerances and Surface Finish
Applications of On-Demand Moulding
Several factors affect moulding tolerances and surface finish in on-demand production, including:
- Material selection: Different materials have varying shrinkage rates, affecting tolerances and surface finish.
- Tooling quality: High-quality tooling ensures precise dimensions and surface finishes.
- Manufacturing process: Injection moulding, CNC machining, and 3D printing have unique tolerance and surface finish capabilities.
- Design complexity: Intricate designs can compromise tolerances and surface finish.
Best Practices for Achieving Optimal Results
To ensure optimal moulding tolerances and surface finish in on-demand production:
- Work with experienced manufacturers and designers to optimize part design and material selection.
- Clearly define tolerance and surface finish expectations.
- Choose materials compatible with the desired surface finish and tolerance requirements.
Mechkonnect Industrial Solutions Pvt Ltd is a trusted partner for moulding and on-demand manufacturing projects. With expertise in injection moulding, CNC machining, and 3D printing, Mechkonnect ensures precise moulding tolerances and high-quality surface finishes. By leveraging advanced technologies and collaborating closely with clients, Mechkonnect delivers exceptional results, meeting even the most stringent requirements. Whether you need rapid prototyping or large-scale production, Mechkonnect’s on-demand manufacturing solutions guarantee precision, quality, and reliability.
Partner with Mechkonnect to bring your vision to life with unparalleled accuracy and efficiency.