3D scanning is a transformative technology that captures the physical characteristics of objects or environments and converts them into digital 3D models. This process involves analyzing real-world items to collect three-dimensional data regarding their shape, texture, and sometimes color. The resulting data can be utilized across various industries, enabling reverse engineering, quality control, and virtual reality applications.
How 3D Scanning Works
The core functionality of a 3D scanner is to create a digital representation of an object. This is achieved through several key steps:
- Data Acquisition: A 3D scanner emits a beam of light or uses multiple photographs to capture the object from various angles. Technologies like laser scanning, structured light, and photogrammetry are commonly employed for this purpose.
- Point Cloud Creation: As the scanner collects data, it generates a “point cloud”—a collection of data points that represent the surface of the object in three-dimensional space. Each point in this cloud corresponds to a specific location on the object’s surface, allowing for detailed representation.
- Model Reconstruction: The point cloud data is processed using specialized software to create a polygon mesh or a complete 3D model. This model can then be manipulated or analyzed for various applications.
- Alignment and Merging: In cases where multiple scans are necessary to capture all aspects of an object, these scans must be aligned and merged into a single cohesive model, a process known as registration.
Technologies Used in 3D Scanning
There are several technologies employed in 3D scanning, each with its advantages and limitations:
Laser Scanning: This technique uses laser beams to capture precise measurements of an object’s surface. Laser scanners can gather millions of data points quickly and accurately, making them ideal for complex geometries.
Structured Light Scanning: This method projects a series of light patterns onto the object and captures the deformation of these patterns to create a 3D model. It is particularly effective for capturing fine details on small objects.
Photogrammetry: Utilizing multiple photographs taken from different angles, this technique reconstructs a 3D model by analyzing overlapping images. It is often used in applications where detail is crucial but high precision is not as critical as with laser scanning.
LiDAR (Light Detection and Ranging): Commonly used in topographical mapping and large-scale environmental scanning, LiDAR employs laser pulses to measure distances between the scanner and the target surface, generating highly accurate spatial data.
Applications of 3D Scanning
The versatility of 3D scanning technology allows it to be applied across numerous fields:
- Manufacturing and Engineering: Used for quality control, reverse engineering, and designing complex parts with high precision. 3D scanning works effectively when paired with advanced 3D printing machines for rapid prototyping and streamlined production workflows.
- Entertainment: In film and video game production, 3D scanning creates realistic digital models for characters and environments, enhancing visual effects.
- Healthcare: Custom prosthetics and orthotics can be designed using accurate scans of patients’ body parts, ensuring better fit and functionality.
- Cultural Heritage: Museums utilize 3D scanning for digital preservation of artifacts, allowing for virtual exhibitions without risking damage to original items.
- Architecture and Construction: Architects use 3D scanning for site analysis and creating accurate models of existing structures for renovation projects.
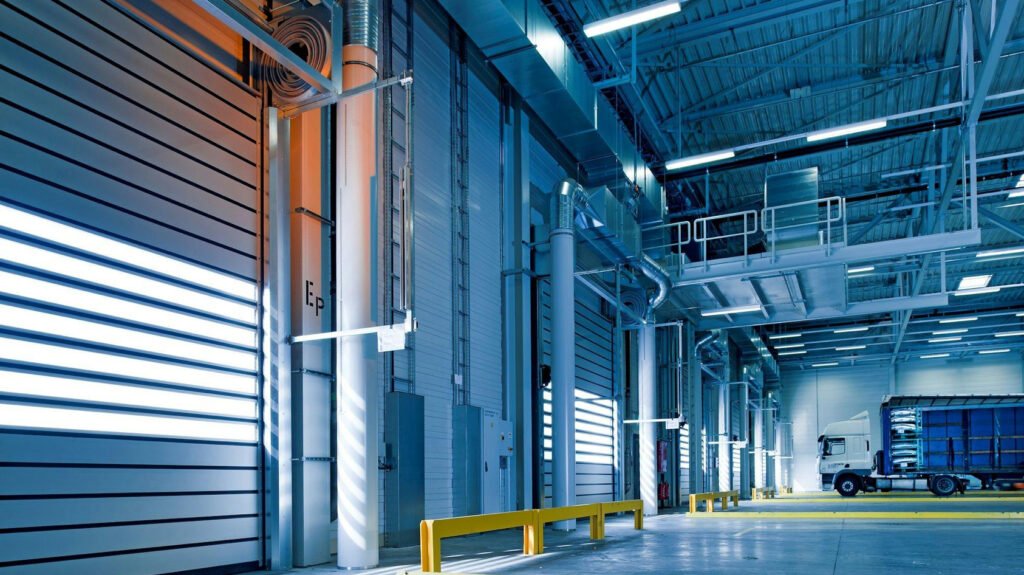
Benefits of 3D Scanning
The adoption of 3D scanning technology offers several advantages:
- Captures intricate details with remarkable precision, which is essential for high-quality manufacturing processes.
- Streamlines traditional measurement methods, significantly reducing the time required to capture complex shapes.
- Minimizes labour costs associated with manual measurements and inspections while improving overall productivity.
- Facilitates rapid verification against design specifications, helping identify deviations early in the production process.
- Facilitated Reverse Engineering: Simplifies the process of understanding existing products by providing accurate dimensional data for redesign or reproduction purposes.
- 3D scanning is highly compatible with 3D printing machines, allowing scanned models to be directly translated into physical objects.
In summary, 3D scanning represents a significant advancement in how we digitize and interact with the physical world. Its applications span numerous industries—from manufacturing to cultural preservation—demonstrating its versatility and importance in modern technology. As advancements continue in scanning technologies and software algorithms, the potential for even broader applications will likely expand further.
Learn more about our 3D printing and scanning services!
Forward-looking Statements
This press release contains forward-looking statements within the meaning of the Securities Act of 1933 and the Securities Exchange Act of 1934. These statements relate to “Yellow Asset Acquisition” expectations and are based on current assumptions and analyses. Forward-looking terms such as “anticipate,” “estimate,” “expect,” and similar expressions indicate such statements. These statements are subject to various risks and uncertainties, including factors outlined in Swift Line’s filings with the Securities and Exchange Commission (SEC) and risks related to the ongoing Yellow bankruptcy proceedings and the integration of the acquired assets.
3D scanning stands as a pivotal technology in the modern digital landscape, bridging the gap between physical objects and their digital counterparts. When used alongside 3D printing machines, it revolutionizes the way industries approach design, prototyping, and production. As the technology continues to evolve, its applications are set to expand, offering even more innovative solutions across various sectors.
Swift Line cautions that actual results may differ materially from those projected in forward-looking statements owing to factors like economic conditions, regulatory challenges, labor shortages, fuel price fluctuations, and other risks. Swift Line assumes no obligation to update forward-looking statements except as law requires.