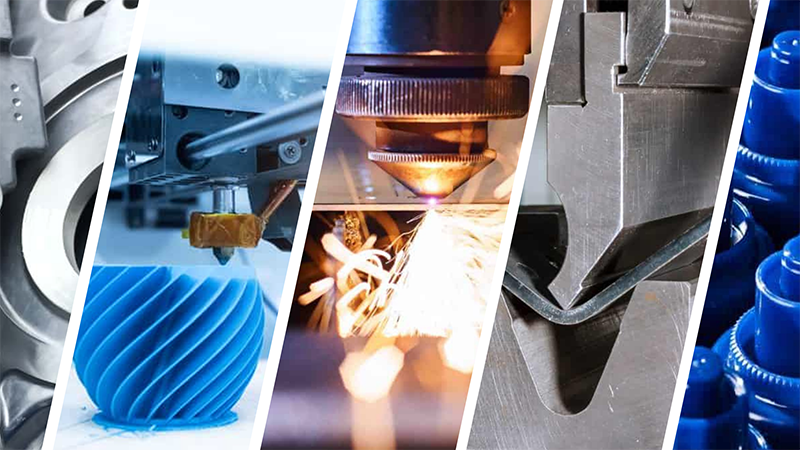
There’s a growing need for creating custom parts and products at lightning speed in ever-advancing manufacturing industries. On-demand Fabrication of metal has revolutionized the industry, enabling companies to quickly respond to changing market needs and customer demands. This shift towards agile manufacturing has placed a premium on efficient and effective fabrication processes. Among these processes, welding plays a crucial role in joining materials together to create strong, durable, and high-quality products. With various welding techniques available, selecting the right one can be an intimidating task.
In this article, we will explore the basics of welding, and its applications, and delve into three primary welding techniques used in on-demand fabrication: TIG, MIG, and Arc welding.
What is Welding?
Welding is a fabrication process that creates a strong and durable joint between two metal parts. It offers numerous benefits, including high-strength bonds, versatility in joining various materials, cost-effective fabrication, enhanced product design flexibility, and improved product lifespan. Fabrication of metals through welding is a critical process in industries such as automotive, construction, and aerospace, where precision and durability are essential.
Applications of Welding
Welding has numerous applications across industries. In construction, welding is used to build frames, bridges, and pipelines. In the automotive industry, welding is used to manufacture vehicle chassis, engines, and exhaust systems. The aerospace industry relies on welding to create aircraft structures and engine components. Additionally, welding is used in manufacturing to produce equipment, machinery, and consumer goods.
TIG (Tungsten Inert Gas) Welding Technique
TIG welding also referred to as Gas Tungsten Arc Welding (GTAW), employs a non-consumable tungsten electrode to generate accurate and high-quality welds. This technique involves creating an electric arc between the tungsten electrode and the workpiece while shielding the area with an inert gas. TIG welding is ideal for welding thin materials, producing intricate welds, and achieving high purity and cleanliness.
MIG (Metal Inert Gas) Welding Technique
MIG welding, also known as Gas Metal Arc Welding (GMAW), is a highly efficient welding method that utilizes a consumable wire electrode and an inert gas to swiftly create robust welds. This technique involves continuously feeding a wire electrode through a gun, which creates an electric arc when it contacts the workpiece. MIG welding is suitable for welding thicker materials, high-volume production, and faster welding speeds.
– Axles and shafts
Arc Welding Technique
Arc welding, also known as Shielded Metal Arc Welding (SMAW), uses a consumable electrode covered in flux to produce a robust, versatile weld. This technique involves creating an electric arc between the electrode and the workpiece, while the flux shields the area and produces a slag that protects the weld. Arc welding is ideal for thick material welding, repair and maintenance applications, and outdoor or field welding.
Choosing the Right Welding Technique
When selecting a welding technique for on-demand fabrication on metal, it is essential to consider factors such as material type and thickness, desired weld quality and appearance, production volume and speed, and operator skill level.
Mechkonnect Industrial Solutions Pvt Ltd: Your Partner in Welding On-Demand Manufacturing Projects
For businesses seeking expertise in welding on-demand manufacturing projects, Mechkonnect Industrial Solutions Pvt Ltd is an ideal partner. With extensive experience in TIG, MIG, and Arc welding techniques, their team of skilled professionals can help optimize your fabrication process, improve weld quality and consistency, increase production efficiency, and reduce costs and lead times. By collaborating with Mechkonnect Industrial Solutions Pvt Ltd, you can leverage their expertise to streamline your welding operations and deliver high-quality products to your customers.
Ready to ignite your welding components? Start your project with us today!