Computer Numerical Control CNC machines have revolutionized the field of fabrication by providing unmatched precision, efficiency, and versatility. CNC machines have become essential tools in industries ranging from aerospace and automotive to medical and art, enabling manufacturers to create intricate and accurate components with ease. The introduction of Computer Numerical Control (CNC) technology in the field of fabrication marked a significant turning point in the way products are designed and manufactured. CNC machines are computer-controlled tools that precisely cut, shape, and assemble materials such as metal, plastic, wood, and composites. The ability to program CNC machines with digital instructions has led to unparalleled levels of accuracy and repeatability in fabrication processes. This article provides a comprehensive overview of CNC machines, their principles, types, applications, advantages, and future developments.
Historical Perspective
CNC technology traces its origins back to the mid-20th century when the need for automated machining processes became apparent. The earliest CNC systems were rudimentary compared to modern standards but paved the way for the evolution of precision manufacturing. Numerical control systems were first used in the aerospace and defence industries during the 1950s. The first CNC machines tool, a milling machine, was developed in 1952 at the Massachusetts Institute of Technology (MIT).
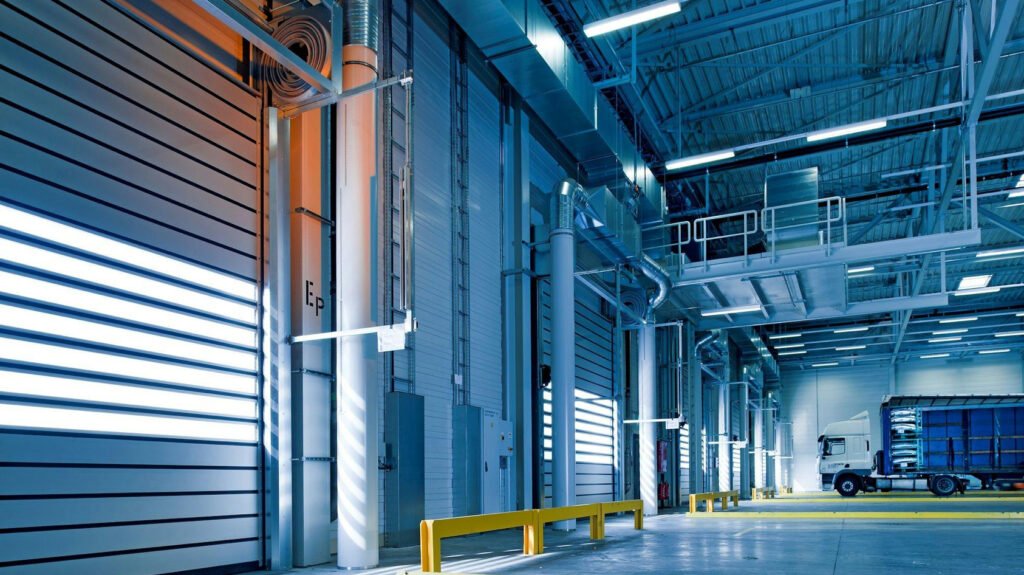
Principles of Operation
At its core, CNC machining relies on a set of precise instructions generated through Computer-Aided Design (CAD) software. These instructions, often referred to as G-codes and M-codes, are fed into the CNC machine’s controller. The controller interprets these codes and directs the machine’s movements, which typically involve the positioning of a cutting tool or workpiece along multiple axes (X, Y, Z).
The primary components of a CNC machine include:
Controller
The brain of the CNC system is responsible for interpreting the G-code instructions and generating signals for the motors.
Tool or Workpiece Holder
Depending on the specific CNC machine type, this component holds the cutting tool or the workpiece being processed.
Feedback Systems
Encoders and sensors provide real-time feedback to ensure precise positioning and adjustments during machining.
Cutting Tool
In milling and machining centres, the cutting tool rotates and removes material. In other CNC machines like lathes, the tool moves along the workpiece to achieve desired shapes.
Types of CNC Machines
CNC technology has spawned a wide variety of machine types, each tailored to specific fabrication needs. Some common types include:
- CNC Milling Machines
They are ideal for producing complex 3D shapes and are commonly used in the aerospace and automotive industries.
- CNC Lathes
Lathes rotate the workpiece while a cutting tool moves parallel to the workpiece’s axis. They are suitable for creating cylindrical or conical shapes, making them essential in the production of shafts and bolts.
- CNC Plasma Cutters
Plasma cutters use a high-velocity jet of ionized gas to cut through materials like metal and steel. They are widely used for metal fabrication and industrial applications.
- CNC Laser Cutters
These machines utilize lasers to cut, engrave, or mark various materials, including metal, wood, and plastic. They are highly precise and find applications in the electronics and jewellery industries.
- CNC Waterjet Cutters
Waterjet cutters employ a high-pressure stream of water mixed with abrasive particles to cut a wide range of materials, from foam to titanium.
- CNC 3D Printers
While not traditional subtractive CNC machines, 3D printers with CNC-like capabilities can create complex 3D objects by adding material layer by layer. They are used extensively in rapid prototyping and customized production.
Applications of CNC Machines
CNC machines have found their way into numerous industries, and their applications are diverse:
- CNC machining is crucial for fabricating precision components like aircraft engine parts and aerospace structures.
- CNC machines produce engine components, transmission parts, and intricate body panels with high precision.
- CNC technology is used to create custom implants, dental prosthetics, and medical instruments, ensuring a perfect fit for patients.
- Artists and sculptors use CNC machines to bring their intricate designs to life, working with materials ranging from wood to stone.
- Circuit boards, enclosures, and small precision parts are manufactured using CNC technology.
- CNC routers are employed to craft fine furniture, cabinetry, and decorative woodwork.
- Intricate jewellery designs are made possible with CNC engraving and milling machines.
- CNC machines are instrumental in the rapid prototyping of new products and components.
Advantages of CNC Machines
The adoption of CNC machines in fabrication processes offers several key advantages:
- Precision
CNC machines can achieve levels of precision and repeatability that are nearly impossible to replicate manually.
- Efficiency
Automation reduces the risk of errors, minimizes material waste, and accelerates production times.
- Complexity
CNC machines can create intricate and complex shapes that would be extremely challenging to produce by hand.
- Flexibility
With reprogramming, CNC machines can switch between different tasks and materials quickly.
- Cost-Effectiveness
While initial investment costs can be high, the long-term cost savings in labour and materials make CNC machining economically viable.
Future Prospects and Emerging Trends
As technology continues to advance, CNC machines are likely to evolve and become even more powerful and versatile. Some emerging trends include:
Additive Manufacturing Integration
Combining CNC machining with additive manufacturing techniques enables hybrid machines that can both add and subtract material, expanding design possibilities.
Artificial Intelligence (AI) and Machine Learning
AI-driven CNC systems can optimize tool paths, detect defects, and adapt to changing conditions in real-time.
Nanotechnology
CNC machines are advancing into the nanoscale, enabling the fabrication of microdevices and components with unprecedented precision
Sustainability
CNC machining is becoming more environmentally friendly, with innovations in materials recycling and energy-efficient processes.
Remote Monitoring and Control
IoT integration allows for remote monitoring and control of CNC machines, improving maintenance and reducing downtime.