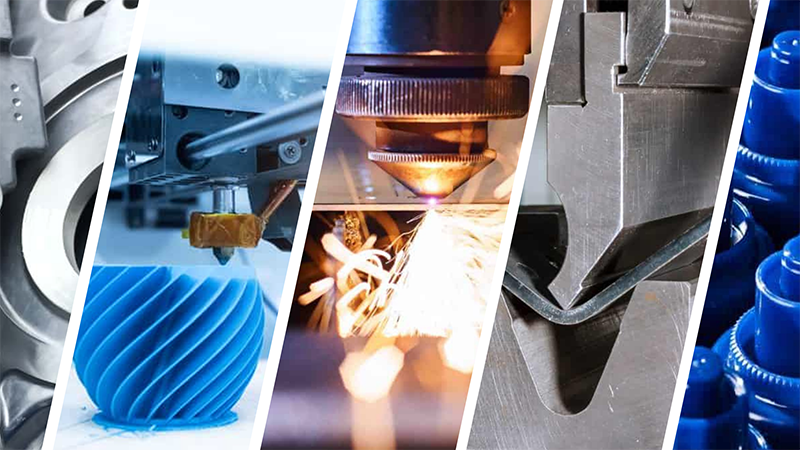
Innovation is the heartbeat of progress. And with the Internet of Things (IoT) smart manufacturing has emerged as a powerful force across industries. The digital era has ushered in an interconnected world, where everyday objects communicate, adapt, and respond intelligently. Meanwhile, on-demand manufacturing disrupts traditional supply chains, challenging the status quo by producing goods precisely when needed.
This article delves into the symbiotic relationship between these two domains, exploring their impact, advantages, challenges, and limitations.
This article explores the concept and process of on-demand manufacturing in sheet metal fabrication for the automotive sector, elucidating its benefits and transformative potential for the larger and advancing automotive field. But first, we will go on to explore the fundamentals.
Understanding IoT Devices
Before we delve into the specifics, let’s establish a foundational understanding of IoT devices.
These interconnected smart devices collect, transmit, and process data autonomously. They range from tiny sensors embedded in everyday objects to complex machinery in industrial settings.
Key characteristics of IoT devices include:
Connectivity: IoT devices communicate via wireless networks (e.g., Wi-Fi, Bluetooth, cellular) or wired connections.
Sensing Capabilities: Sensors capture real-time data (temperature, humidity, motion, etc.) from the environment.
Data Processing: IoT devices process data locally or in the cloud, enabling informed decision-making.
Automation: They trigger actions based on predefined rules or algorithms.
On-Demand Manufacturing: A Paradigm Shift
On-demand manufacturing disrupts traditional supply chains by producing goods only when needed. Key aspects include:
Role of IoT in On-Demand Manufacturing
IoT devices play a pivotal role in shaping on-demand manufacturing:
Real-Time Monitoring: Sensors track machine performance, inventory levels, and product quality. Manufacturers can adjust production dynamically.
Predictive Maintenance: IoT-enabled predictive analytics prevent equipment breakdowns, reducing downtime.
Supply Chain Visibility: IoT devices provide real-time data on raw material availability, transportation, and logistics.
Quality Assurance: Sensors monitor product quality during production, ensuring adherence to standards.
Advantages of the IoT-On-Demand Manufacturing Nexus
Efficiency: Real-time data enables efficient resource allocation, minimizing waste.
Cost Reduction: Predictive maintenance reduces unplanned downtime and repair costs.
Personalisation: IoT-driven customization enhances customer satisfaction.
Traceability: End-to-end visibility ensures transparency and accountability.
Challenges and Limitations
The synergy between IoT devices and on-demand manufacturing reshapes how products are conceived, produced, and delivered. As technology advances, companies must strike a balance between innovation and risk mitigation. The future lies in harnessing the power of IoT to create a more responsive, sustainable, and customer-centric manufacturing ecosystem.
In summary, the marriage of IoT and on-demand manufacturing is not just a trend—it’s a transformative force that propels us toward a smarter, more efficient industrial landscape.
MechKonnect was born out of these problems to cater Industry’s needs and requirements. We have a developing network of vendors across services such as Fabrication, Machining, Casting, and 3D Printing. Within a short span, we have already catered to clients across domains such as Oil and Gas, Construction, Power just to name a few.